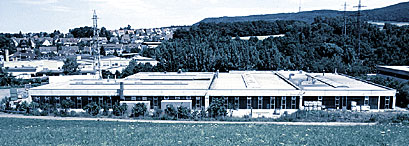
PROGRESS HAS A NAME: COMPETENCE
Continuous development work and investments in modern production facilities brought up ROWA to be one of the most important producer of non-woven products.
By using different manufacturing and stabilization methods, ROWA is developing and producing needle-felts, HF-welding-fleeces, wool-waddings, quilt-fleeces, filter-fleeces and fleeces for the use of heat and sound absorption. ROWA products are used in automotive seats and in the automotive interior as sound absorbing insulation parts and comfort giving paddings, upholstery, interlayers and also in quilt covers, cushion fillings and clothing textiles.
On the production area extending over 26,000 square meters several thousand tons of raw material are processed annually.
No matter if the raw material is fixed mechanically or thermally - all these processes have an optimal environmental compatibility.
The fleeces produced by the most up-to-date equipment are subject to the most rigid quality checks. These tests are effected not only by textile-technicians at ROWA they are also top-priority.
Our CAD technique allows us to communicate online with our OEMs and system-suppliers so all technical data can be mutually integrated and postprocessed.
Manufacturing methods of our fleece qualities in detail
To produce high-quality products ROWA is using the following different techniques of fixation.
Mechanical stabilization: This method bases on mechanical fiber entanglement by needling. These tear proof needle felts, are used basically as technical felts like filter felts and lordose felts. Soft and voluminous versions are delivered to the automotive industry and their system suppliers.
Thermobonding: The thermobonding method uses melting fibers to manufacture extremely voluminous and dimensionally stable fleeces. Thin fiberwebs are laid over each other crosswise. They are condensed by pressure rollers and become heated up in an oven, causing the melting fibers to interconnect. Such kind of fixed fibers are used for automotive acoustic fleeces and filter media. Special fiber orientations are used for vertically attached fleeces to create foam substitutes.
Additional fleece finishing
Hotmelt-laminations: By using thermoplastic powder or lamination-foil, our fleeces are bonded with materials like fabrics, knitted fabrics or spunbonds to stabilize our fleeces, e. g. to support sewing and also to avoid fiber migration.
Fleece confection: On our punches and cutters we produce pre-cut parts for the processing industry, e. g. seat cover manufacturers in the automotive industry and also for the automotive producers.
|